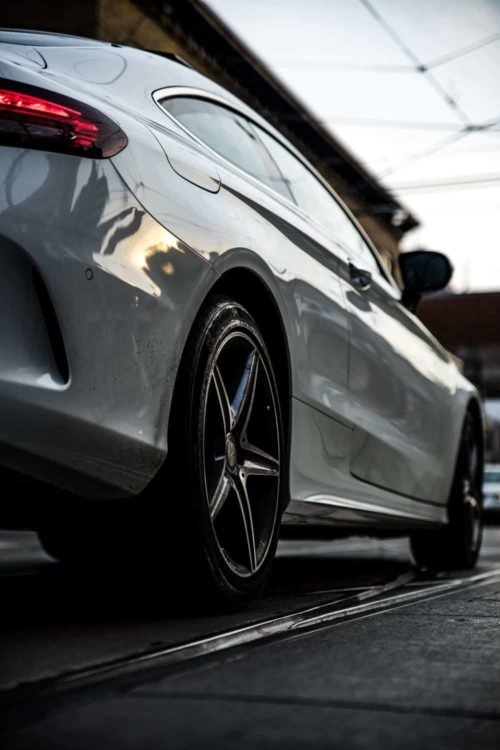
Body structures Truck Liftgates
Composites are growing in use for many advantages of weight and flexibility, and in many cases their effectiveness and safety depend on adhesive bond quality.
Manufacturing requires stringent surface preparation and consistent application and curing.
The development of Laser Bond Inspection fills a key gap, providing non-destructive testing to assure quality adhesive bond performance.
The Challenge
Take full advantage of composite structures
The solution
Employ tailored laser-induced high amplitude stress waves that will
Delivering Precision
Composite designers promise that unitized structures will provide high-strength, low-weight, and low-cost components that will outperform equivalent metal parts in cost and efficiency.
But without adequate testing to fulfill that promise, many composite parts with adhesive bonds are in fact also reinforced with nuts, bolts, and rivets. Their adhesive is treated as an environmental sealant, rather than a bonding adhesive.
It’s easy to understand the complications. Composite adhesives involve a complex set of variables in surface preparation, consistent application, and cure time, often depending on manual processes.
Laser Bond Inspection attacks these issues head on, providing non-destructive testing to composite adhesives during component production, post-assembly, and even in maintenance and overhaul operations.
With Laser Bond Inspection, the goal of verifiable quality for composite adhesive bonds is now in reach, adding new possibilities for these unitized structures.
Body structures Truck Liftgates
Wing and Fuselage Structures Scarf and Boron Patch Repairs
Wind Turbine Blades
Heat resistant coatings Metal-to-metal Metal-to-composites Composites-to-composites
Less expensive than conventional full-scale testing, Laser Bond Inspection provides real-time quality assurance for composite adhesive bonds during all phases of production -- even after assembly or in maintenance and repair environments. . LBI also detects kissing bonds -- composite layers touching without mechanical strength -- a key capability missing from ultrasonic testing.
Major aerospace manufacturers and defense aviation experts now agree Laser Bond Inspection has the potential to dramatically improve quality insurance for composite adhesive bonds.
The excitement now extends to commercial customers in a wide range of industries with their own demanding composite bond applications. Laser Bond Inspection provides the precision and ease-of-use you would expect from LSP Technologies.
To find out more about Laser Bond Inspection, please tell us a little about your application, and our highly qualified application development consultants will develop a cost-effective plan to improve quality assurance for your composite bond application.